試作
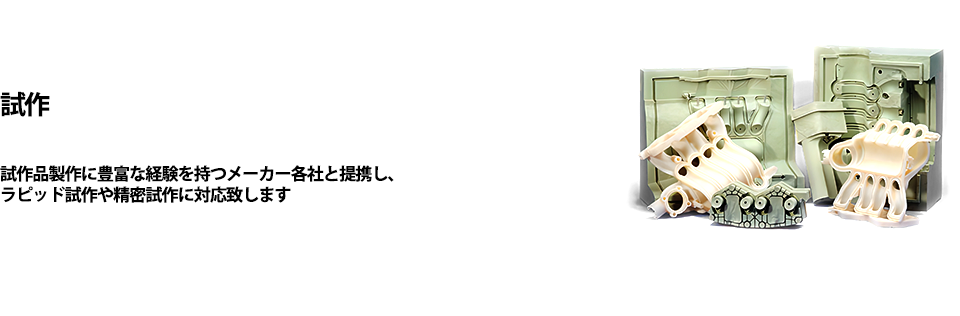
ファイバーレーザー溶融造形
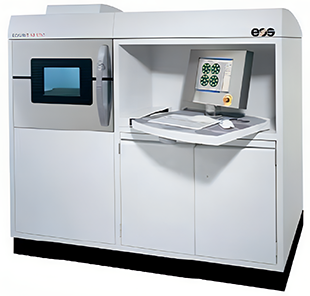
概要
レーザーで金属パウダーを溶融し、3D形状に造形する新技術です。つまり、ダイレクトに部品を造形できるので、型が不要です。 また、型そのものを造形し、“金型”として使うことも可能です。
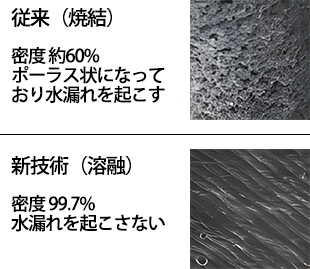
特徴
- 新技術は世界No.1の造形密度(99.7%) > 従来技術(60%)
- 形状に制限がありません(複雑な水冷管も製作可能)
- 残留応力を残さない独自の造形手法を開発
- 技術的に優位性の高いファイバーレーザーを使用(従来はYAG)
- 材料の種類も世界No.1
製品適用例
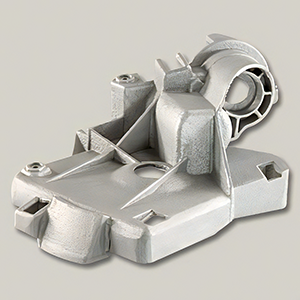
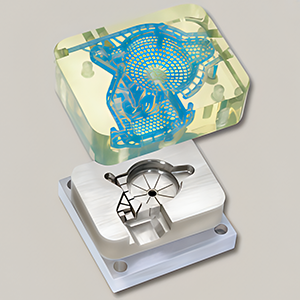
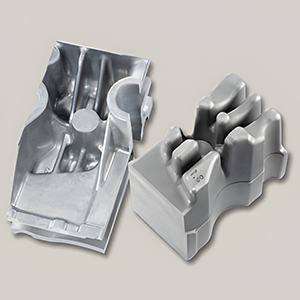
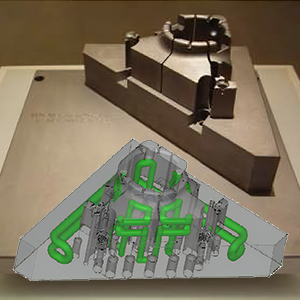
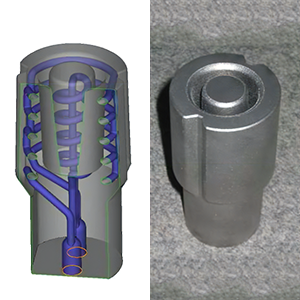
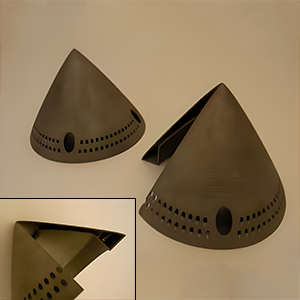
鋳造試作
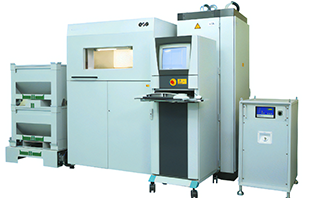
技術の特徴
- ラピッドプロト装置を使った焼結積層砂型の自動製作を実現
効果 : 従来の砂型が不要 ⇒ リードタイムを大幅短縮 - 焼結積層砂型は、3D製品データを忠実に再現
効果 : 製品強度や形状、肉厚などの詳細評価が可能
(従来砂型は3D製品データと細部形状が異なる)
適用部品
1~数個のAL鋳造部品
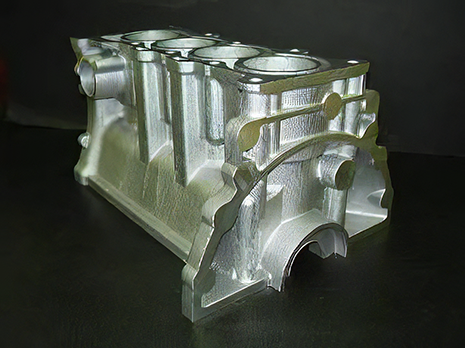
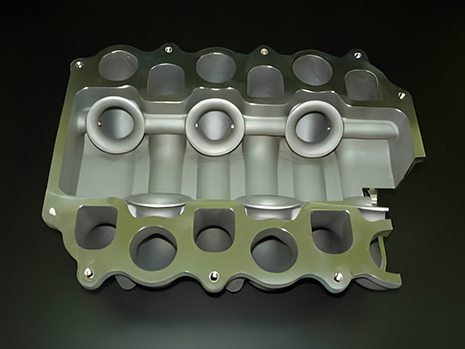
樹脂試作
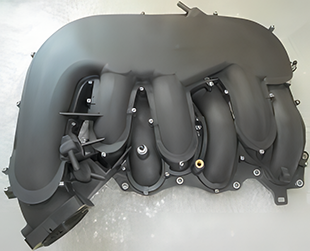
技術の特徴
- 真空注型を用いたウレタン材のインマニを実現
効果 : 従来は樹脂インジェクション金型を製作
⇒ 真空注型によりコスト・リードタイムを大幅削減
⇒ 耐熱性に優れ、エンジン単体試験に適用化
耐熱性:160℃
ヤング率:1,940MPa
納期:最短2.0週間
コスト:型費60%カット
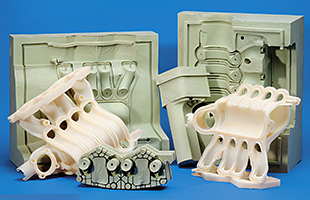
- 真空注型を用いたナイロン材のインマニを実現
効果 : 従来は樹脂インジェクション金型を製作
⇒ 真空注型によりコスト・リードタイムを大幅削減
⇒ 剛性・耐熱性に優れ、車輌搭載試験に適用化
耐熱性:230℃
ヤング率:5,200MPa
納期:最短2.0週間
コスト:型費60%カット
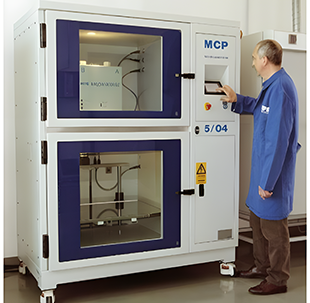
製作技術のポイント
- 寸法検査
3Dレーザー計測によるCADとの比較検査を実施後、納品いたします。 - 接着方法
着材(スリーボンド)+液体ガスケットを使用、リーク検査後、納品いたします。 - 収縮率の管理
3Dレーザー計測によるCADとの比較、はめこみ収縮率を考慮した寸法管理を実施しております。 - 材料開発(強度UP)
PA3000GF30(ガラスフィラーを30%配合)を開発!PA3000(未配合)に対しヤング率2.0倍以上
その他工法の御紹介
- 光造形
光造形による試作モデル加工法とは、3Dデータ(STL)を利用して、材料となる光硬化樹脂(エポキシ系樹脂が主)に紫外線レーザーを当て試作モデルを積層造形する試作方法。 - 粉末造形
粉末造形による試作モデル加工法とは、3Dデータ(STL)を利用して、粉末(PA・PP・ゴム・スチレン・砂・金属等)にレーザービームを当て積層造形する試作加工方法。デザインモデルだけでなく、粉末造形による試作モデルは、ワーキングモデル(評価試験)としても利用可能。 - 機械加工
切削による試作モデル加工法 は、マシニング・旋盤・フライス等で、素材を削って加工する方法。 - 射出成形(簡易金型)
射出成形による試作モデル加工法は、主にアルミ・鉄材・ZASの金属系素材で キャビ・コア部分のみを試作し、射出成形する加工法。 - 石膏鋳造
マスターモデルにより石膏型を作成し、溶解状態の金属(アルミ・亜鉛・マグネシウム)を流し込み製品を得る方法。マスターモデルの複製品を作る試作技法 。
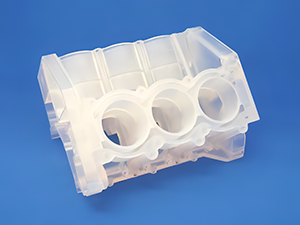
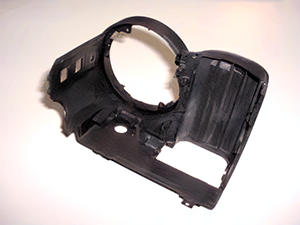
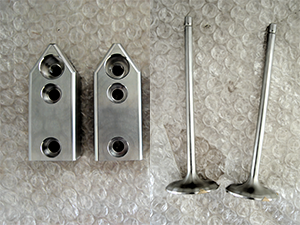
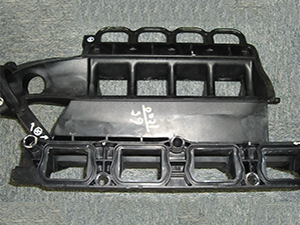
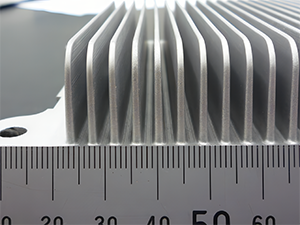